اگر با ابزارهای دستی یا ماشینی سروکار دارید تقریباً تضمینی میتوان گفت از چیزی استفاده کردهاید که سخت شده است؛ سختکاری سطحی برای تقریباً هر صنعتی یک فرآیند حیاتی است، از نجاری گرفته تا تولید انرژی هستهای.
همانطور که در مقالات قبلی بررسی کردیم انواع مختلفی از سخت شدن وجود دارد که یکی از آنها سخت شدن سطحی است. در این مقاله از فولادینو بهطور دقیقتر بررسی میکنیم که سخت شدن سطح چیست و چگونه انجام می شود؟
فهرست این مطلب
سخت شدن چیست؟
سختی معیاری است که نشاندهنده میزان مقاومت یک ماده در برابر سایش و خراش است و فرآیند سخت شدن برای بالا بردن این سطح و افزایش توانایی یک قطعه برای عملکرد در محیطهای ساینده انجام میشود.
انواع مختلفی از سخت شدن وجود دارد، از جمله سخت کاری کامل و سخت کاری سطحی. هر دوی این روشها را میتوان روی طیف وسیعی از فلزات مختلف اعمال کرد؛ هرچند که یکی از رایج ترین آنها فولاد کمکربن است.
سخت کاری سطحی چیست؟
همانطور که از نام آن پیداست سفت کاری سطحی، سخت شدن مواد در سطوح بیرونی یک قطعه را نشان میدهد به طوری که داخل آن در سطح سختی طبیعی ماده باقی مانده باشد.
از آنجاییکه سختکاری سطحی اغلب به طور چشمگیری انجام ماشینکاری و سایر کارها را بر روی قطعه دشوار می کند، این عمل به عنوان یکی از آخرین مراحل فرایند تولید انجام می شود.
بیشتر بخوانید: معروفترین روشهای پوششدهی فلزات کدامند؟
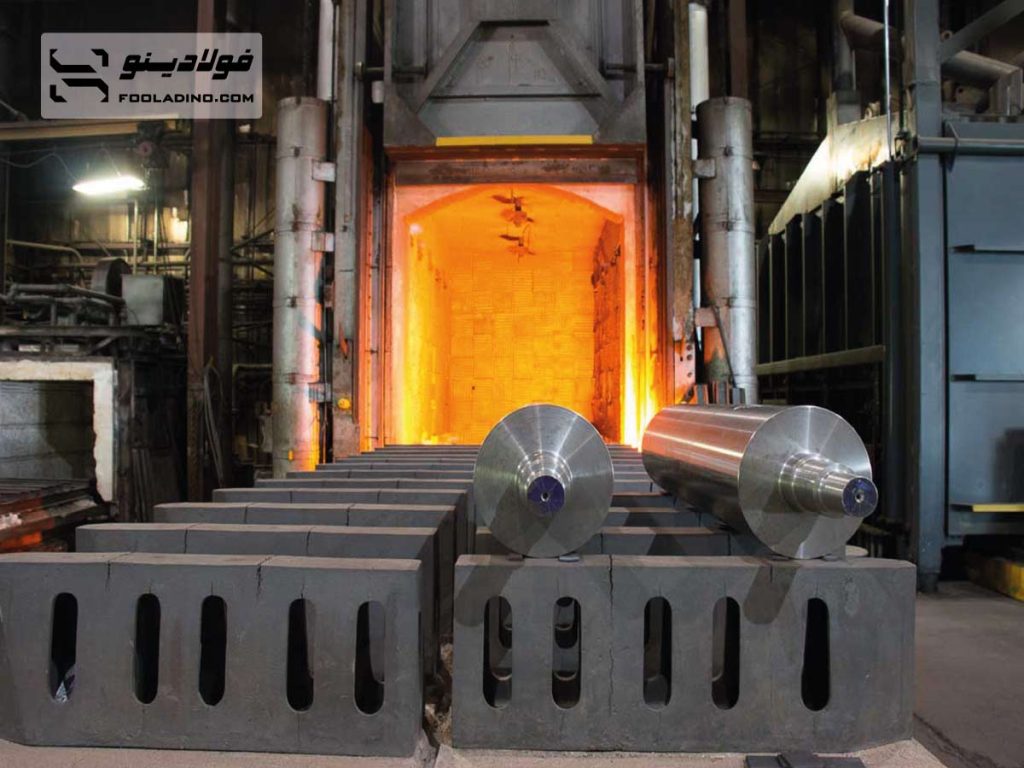
تکنیکهای سختکاری سطح
برای اینکه بتوان فرایند سختکاری را بر روی قطعاتی از جنس و شکلهای مختلف اعمال کرد تکنیکهای متعددی توسعه داده شدهاند که هر کدام مزایا و معایب خاص خود را دارند. در ادامه تعدادی از آنها را مورد بررسی قرار خواهیم داد:
کربورسازی
کربورسازی قدیمیترین تکنیک سختکای سطحی است و به روش افزایش محتوای کربن فلز در سطح، با حرارت دادن در دماهای بالا در یک محیط غنی از کربن عمل میکند. لایه سختی که نهایتا حاصل میشود معمولا بین ۱ تا ۲ میلیمتر ضخامت دارد.
آهنگران قرون وسطایی یاد گرفته بودند که باقی گذاشتن تیغه در یک فورج زغال سنگ برای ساعتها، سختی قابل توجهی به فولاد اضافه میکند. فرایندی که گمان میرود یک نسخه ابتدایی از کربورسازی باشد.
امروزه این فرآیند بسیار کنترل شده انجام میشود. کوره های الکتریکی قطعات را در دمای مورد نیاز نگه میدارند و از خمیر و محصولات قدرتی خاص برای افزودن کربن استفاده میشود.
فواید کربورسازی
- هزینه: به مواد یا تجهیزات نسبتا کمی نیاز دارد.
- مقیاس: بعد از مشخص کردن پارامترهای فرآیند، میتوان آن را به صورت انبوه انجام داد.
- تطبیقپذیری: بیشتر فولادها و آلیاژهای آهن را میتوان از طریق کربوریزه شدن سخت کرد؛ حتی اگر کم کربن باشند.
محدودیتهای کربورسازی
- اکسیداسیون: افزایش محتوای کربن و گرما میتواند در شرایط نامناسب باعث اکسیداسیون شود.
- اعوجاج: سطوح بالای حرارت میتواند باعث ایجاد تاب روی اشکال و ضخامتهای خاص قطعات شود.
- محدوده: کربورسازی به آلیاژهای فولادی محدود میشود.
نیتریدینگ
در این روش با انجام فرایندی مشابه Carburizing، سطح یک قطعه را با قرار دادن آن در یک محیط با نیتروژن بالا سفت میکند. افزودن نیتروژن به مواد، نیتریدهایی را تشکیل میدهد که فوقالعاده سخت هستند و مقاومت در برابر سایش و خراش قطعه را به طرز چشمگیری افزایش میدهند.
نیتریدینگ در دمای بسیار پایینتری نسبت به Carburizing، در حدود ۵۲۰ درجه سانتیگراد انجام میشود. همین امر باعث میشود که احتمال کمتری برای ایجاد تغییرات ابعادی یا تاب برداشتن وجود داشته باشد. نیترید کردن باعث ایجاد یک لایه سخت شده بین ۰.۰۵ تا ۰.۵ میلیمتر میشود.
فواید نیتریدینگ
- مقاومت حرارتی: قطعات نیترید شده مقاومت حرارتی بهتری نسبت به قطعات کربندار دارند.
- طیف وسیعی از فلزات: نیتریدینگ را میتوان برای بسیاری از فلزات مانند آلومینیوم، تیتانیوم، وانادیوم و غیره انجام داد.
- اعوجاج کمتر: دمای پایینتر فرآیند به معنای تاب برداشتن کمتر است.
محدودیت های نیتریدینگ
- ضخامت: نیترید کردن باعث ایجاد یک لایه بسیار نازکتر از مواد سختشده در مقایسه با کربنسازی میشود.
- هزینه: نیترید کردن معمولاً در دستههای کوچکتری به نسبت کربنسازی انجام میشود. زیرا نیاز به کنترل دقیقتر دما دارد که نتیجتا منجر به افزایش هزینه پردازش میشود.
بیشتر بخوانید: تست سختی برینل و راکول چیست؟
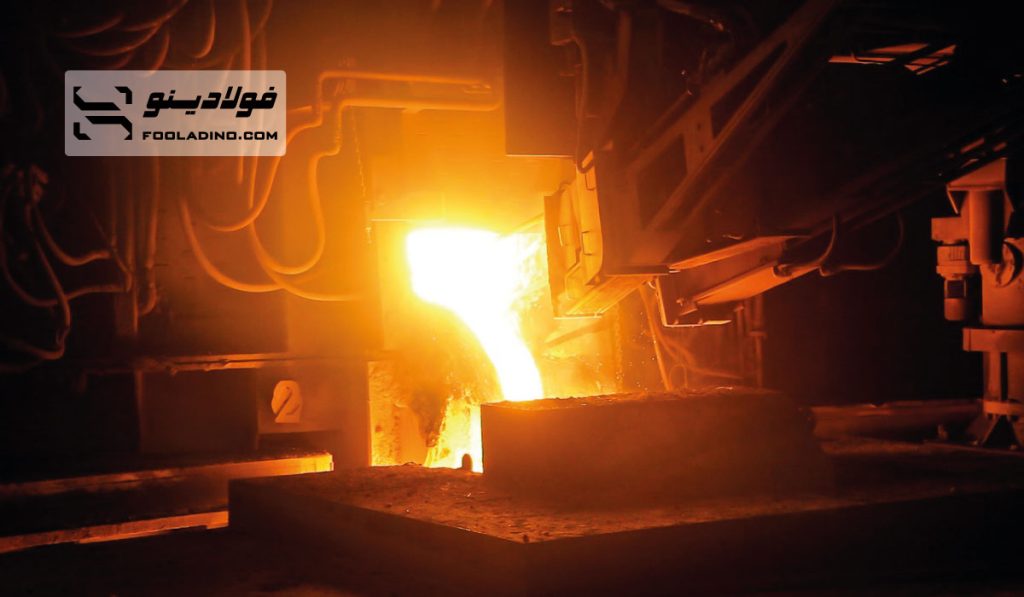
سخت کاری با شعله
اگر مقطع شما کربن کافی داشته باشد، میتوان آن را بدون افزودن هیچ عنصر دیگری مانند کربن یا نیتروژن، سخت کرد. این نوع فرایند سخت شدن یکی از سادهترین راهها برای سختکاری فولاد پر کربن است؛ هرچند که کاربرد آن محدود است.
همانطور که از اسم آن پیداست سختکاری با شعله به وسیله گرم کردن قطعه با شعله تا دمای آستنیته شدن آن انجام میشود. این کار را میتوان با مشعلهای اکسی استیلن یا اکسی پروپان انجام داد. برای فولاد، عدد دمای آستنیته شدن میتواند از ۶۰۰ تا ۸۰۰ درجه سانتیگراد باشد.
هنگامی که فولاد گرم میشود و بلافاصله در آب فرو میرود، مقدار مارتنزیت تشکیل شده در مواد حاصل افزایش پیدا میکند. مارتنزیت یک فاز بسیار سخت از فولاد است که تحت سرد شدن تدریجی تشکیل نمیشود.
انجام این فرایند یک لایه سخت شده را به ماده یا قطعه اضافه میکند که بسته به سطح حرارت و ضخامت قطعه، بین ۰.۱ میلیمتر تا ۶ میلیمتر میتواند ضخامت داشته باشد.
مزایای سخت شدن شعله
- هزینه: سخت کاری شعله را میتوان با حداقل تجهیزات انجام داد و کنترل آن آسان است.
- کنترل: سخت شدن با شعله امکان کنترل دقیق محل سفت شدن قطعه را فراهم می کند. موضوعی که به بقیه قسمتها اجازه میدهد تا چقرمگی خود را حفظ کنند.
محدودیت های سخت شدن شعله
- طیف محدودی از مواد: این نوع سختکاری فقط روی فولادهای با کربن متوسط یا پر کربن کار میکند؛ یعنی در جایی که کربن کافی برای تشکیل مارتنزیت وجود دارد.
- تاب برداشتن: دمای بالا میتواند قسمتهای خاصی را منحرف کند یا باعث تاب برداشتن شود.
- مقیاس: فرایند سخت کاری با شعله باعث تشکیل یک رسوب سنگین میشود که اغلب نیاز به پردازش بیشتری دارد، مانند سندبلاست یا سنگزنی برای حذف.
سخت شدن القایی
سخت کاری به روش القایی از همان اصول سختکاری شعله استفاده میکند، با این تفاوت که گرمایش به جای شعله توسط یک سیم پیچ القایی تامین میشود. استفاده از این روش اجازه میدهد تا گرمایش بسیار بهتر کنترل شود.
گرمایش القایی در صنعت به عنوان یک روش کارآمد بسیار مورد استفاده قرار میگیرد. استفاده از این روش برای گرم کردن یک قطعه فلزی، نه تنها میتواند موضعیتر از گرمایش شعله باشد، بلکه بسیار کارآمدتر است چونکه انرژی کمی از طریق تشعشعات از دست میرود.
مزایای سخت شدن القایی
- کنترل: فرآیند گرمایش کویل القایی امکان کنترل بالاتری نسبت به حرارت دادن با شعله را فراهم میکند، از جمله ضخامت مواد سخت شده و ناحیهای که باید سخت شود.
- سرعت: به لطف کارایی گرمایش القایی و مقادیر زیادی انرژی قابل انتقال، فرآیند گرمایش سریعتر از سخت کاری با شعله است.
- مقیاس: از آنجایی که فرایند از شعله برای گرم کردن مواد استفاده نمیکند، مقیاس کمتری روی سطح تولید میشود.
محدودیتهای سخت شدن القایی
- هزینه: خرید تجهیزات برای تامین انرژی هزینه بیشتر از گرمایش با شعله/اکسی گاز تحمیل میکند.
- مواد: مانند سخت شدن با شعله، سخت شدن القایی را فقط میتوان بر روی فولاد کربن متوسط یا بالا استفاده کرد.
کاربردهای معمول سخت کاری سطحی
استفاده کردن از فرایندهای سخت کاری در انواع کاربردهای صنعتی، از ابزارهای دستی گرفته تا ماشینآلات سنگین کاربرد دارد. همانطور که در ادامه توضیح داده شده است، هرکدام از فرایندهای سختکاری برای اجزای مختلف مناسب است و کاربرد دارد:
کربورسازی: کاربردهای رایج شامل شفت، چرخ دنده و سایر قطعاتی است که نیاز به مقاومت در برابر سایش و مقاومت در برابر بارهای ضربهای دارند.
نیترید کردن: دریچههای موتور و میل بادامک اغلب با فرآیند نیترید سخت میشوند، زیرا استفاده از این روش میتواند سازگاری ابعادی خوبی را حفظ کند.
سخت شدن شعله: اجسام بزرگتر مانند ابزار و ادوات دستی اغلب با شعله سخت میشوند؛ زیرا تاب برداشتن با قطعات ضخیمتر مشکل کمتری دارد و میتوان این فرآیند را برای حجم بالا به صورت خودکار انجام داد.
سخت شدن القایی: کاربردهای رایج شامل شفتها و چرخدندههای بزرگتر است.